Kilka tygodni temu otrzymałem od get3d.pl próbki materiału Poro-Lay – stosunkowo nowego rodzaju filamentu o dość ciekawych właściwościach. W stanie „surowym” materiał ten jest nieco giętki i posiada przyjemną, nieco chropowatą matową fakturę. Ogólnie nie jest jednak rozciągliwy i bardziej przypomina ABS niż gumę. Za to obiekty wytworzone z niego, po umieszczeniu na jakiś czas w wodzie stają się miękkie i elastyczne. Mimo że jest to eksperymentalny materiał i producent zastrzega, że nie udziela pomocy w korzystaniu z niego, w porównaniu z innymi nietypowymi filamentami używanie go nie jest szczególnie trudne. O tym jak Poro-Lay zachowuje się podczas druku oraz późniejszej obróbki miałem okazję się niedawno sprawdzić na własnej drukarce.
Jak można przeczytać w jednym z wcześniejszych artykułów, twórcą filamentu Poro-Lay jest niemiecki inżynier Kai Parthy, który jest wynalazcą również innych egzotycznych materiałów takich jak Laywoo-D3, LayBrick oraz Bendlay. Sam Poro-Lay występuje w kilku wariantach – Lay-Felt, Ley-Tekkks, Ley-Fomm oraz Gel-Lay, różniących się właściwościami fizycznymi. Charakterystyczną cechą wszystkich jego rodzajów jest użycie do ich produkcji 2 zmieszanych ze sobą substancji – właściwej (trwałej) oraz pomocniczej – rozpuszczalnej w wodzie (PVA). Dzięki użyciu takiej mieszanki, po wydrukowaniu obiektów i odpowiednio długim „wymoczeniu” ich, przedmioty nabierają nowych właściwości.
Do swoich testów otrzymałem Lay-Fomm 60, Lay-Fomm 40 oraz Gel-Lay 505 o średnicy 3 mm. Lay-Fomm można zdobyć w wersji twardszej (60) oraz bardziej miękkiej (40) – numer oznacza tu twardość w skali Shore’a (typu A). Wszystkie filamenty występują w różnych odcieniach koloru biało-kremowego. Po dokładnym ich zmierzeniu okazało się, że faktycznie średnica wynosi 2.71 w przypadku Gel-Lay oraz 2.78 mm dla pozostałych dwóch materiałów (liczone jako średnia z 20 pomiarów w różnych miejscach szpuli).
Testowe modele
Właściwości nowego filamentu testowałem na następujących modelach:
- Kwadratu (a dokładniej prostopadłościanu o wymiarach 20 x 20 x 2 mm)
- Ramki (prostopadłościanu 40 x 40 x 2 mm z wyciętym środkiem)
- Plusa (60 x 60 x 16 mm, o grubości ramion 6 mm)
- Wisiorka (Celtic Trinity Heart)
- Płatka śniegu (Snow Flake 008)
- Rzekotki (Treefrog)
Wszystkie modele drukowałem po pocięciu Slic3rem z ustawieniami:
- Grubość warstwy: 0.2 mm
- Prędkość 50 – 80 mm/s (dla obrysów wewnętrznych i wypełnienia)
- Liczba obrysów – 2 lub 3
- Liczba płaszczyzn dół / góra – 3 / 4
- Wypełnienie: plaster miodu 20%
Drukowanie
Lay-Fomm 60
Na początek postanowiłem wypróbować najtwardszy rodzaj filamentu. Rozgrzałem dyszę drukarki do 220 st. C i przepuściłem przez nią kilka mm materiału. Podgrzewanie stołu ustawiłem standardowo na 80 st. C, i jako pierwszy wydruk puściłem model kwadratu. Po wykonywanych jakiś czas temu próbach z gumowym filamentem (TPE) spodziewałem się różnych kłopotów z odklejaniem obiektu podczas druku, problemami z retrakcją czy równomiernym nakładaniem poszczególnych warstw. Jednak wydruk wyszedł bez żadnych komplikacji. Po kilku minutach, dając szybie przykrywającej stół czas na wystygnięcie, spróbowałem delikatnie oderwać mój przedmiot. Okazało się, że nijak nie da się tego zrobić – obiekt tak mocno przykleił się do szkła, że po kilku próbach podważania go, gdy zdecydowałem się użyć nieco większej siły, przedmiot rozerwał się, pozostawiając pierwszą warstwę nadal przyklejoną do stołu.
O ile samoistne odklejanie się obiektu w trakcie druku jest jednym z bardziej denerwujących problemów podczas korzystania z wielu rodzajów filamentów, w przypadku Poro-Lay sytuacja jest zupełnie przeciwna. Kolejne wydruki puszczałem na zimnym stole, co tylko trochę ułatwiło ich późniejsze odklejanie. Na nic nie zdało się też umieszczanie szyby w lodówce. Dopiero kiedy przy kolejnym wydrukowanym przedmiocie spróbowałem włożyć szybę pod bieżącą wodę, po odczekaniu kilkunastu sekund i delikatnym podważeniu go, wydruk bardzo ładnie odkleił się bez żadnych uszkodzeń.
Żeby nieco osłabić przyklejanie się Poro-Lay do stołu warto też zredukować nieco temperaturę dyszy dla pierwszej warstwy (np. do 180 st. C) oraz zwiększyć nieco przestrzeń między stołem a dyszą w pozycji zerowej. W większości wypadków jednak nadal użycie bieżącej wody, lub ochlapanie wydruku i pozostawienie go na chwilę umożliwia jego bezproblemowe odklejenie.
Jako drugi testowy model wykorzystałem ramkę. Tym razem napotkałem problem z rozklejaniem się pionowych płaszczyzn w obiekcie. Co ciekawe, efekt taki występował tylko przy drukowaniu kilku ramek na raz – tak więc obstawiałbym zbyt małą temperaturę dyszy lub zbyt duże chłodzenie wydruku.
Nie mogąc dokładnie zdiagnozować źródła problemu zostawiłem w spokoju ten model i wydrukowałem kilka sztuk płatka śniegu oraz plusa. Obydwa modele zostały wykonane bez większych problemów – choć ze względu na bardziej skomplikowany wzór odklejenie pierwszego z nich wymagało sporo uwagi.
Na koniec zostawiłem model rzekotki. Niestety jak się okazało, przy drukowaniu przewieszeń Poro-Lay dość mocno zawija się do góry, co skutkowało popsuciem niektórych fragmentów obiektu. Ustawienie pełnego chłodzenia od 4 warstwy oraz zwiększenie liczby obrysów z 2 na 3 niewiele w tym przypadku pomogło. Warto podkreślić, że jest do dość trudny model z mocnymi skosami (pow. 45 stopni) z którym również przy druku z PLA miałem sporo kłopotów.



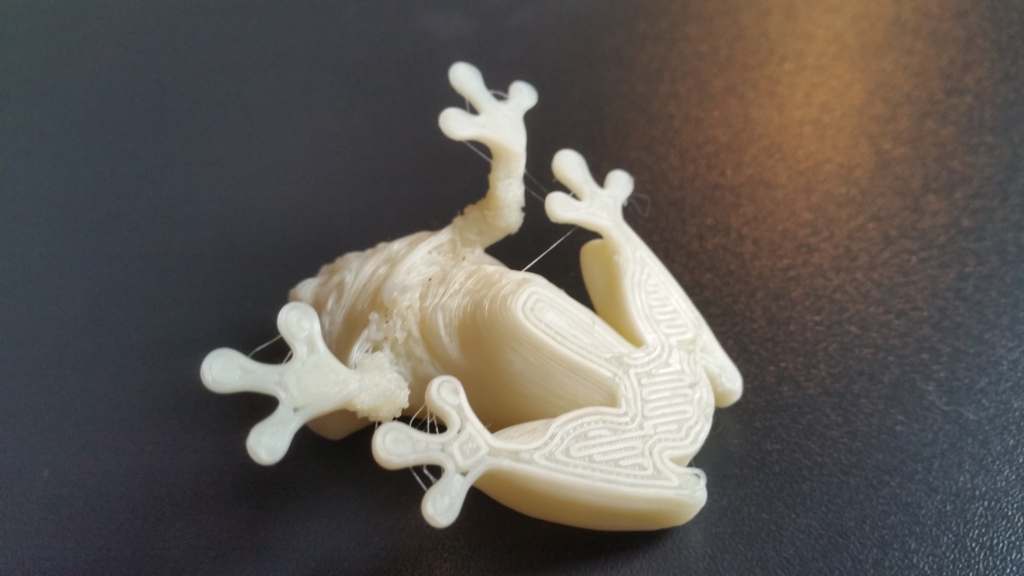
Lay-Fomm 40
Drukowanie z tego materiału specjalnie nie różniło się od pracy z Lay-Fomm 60. Modele wychodziły podobnie i równie trudne okazało się ich odklejanie od szyby. Poza modelem rzekotki, sprawiającej takie same kłopoty jak wcześniej, sam proces drukowania odbywał się bez większych niespodzianek.
Ciekawą cechą Lay-Fomm 40 jest jego samoistne mięknięcie, jeszcze przed samym zanurzeniem w wodzie. Parę godzin po wydrukowaniu przedmioty nabierają wyraźnej elastyczności – co może być bardzo korzystne przy niektórych zastosowaniach. Efekt taki występuje też w przypadku wariantu 60, jednak w trochę mniejszym stopniu.
Gel-Lay
Ostatni z filamentów, zgodnie z zaleceniami od dystrybutora, wymagał nieco większej temperatury druku (230 st. C). Wykonane modele wyraźnie różniły się od obiektów z Lay-Fomm – były całkiem twarde (i nie miękły z czasem), a ich kolor przypominał bardziej przedmioty z żywicy. Niestety odklejenie ich od stołu okazało się jeszcze trudniejsze niż w przypadku Lay-Fomm – tym razem lepszy efekt od odklejania z wodą dało bardzo ostrożne podważanie wydruku cienkim nożykiem do papieru. Oczywiście kilka wydruków udało mi się zepsuć przy tej okazji.




Przy drukowaniu z Gel-Lay dość dobrze wyszedł model rzekotki. Niemal idealnie zostało wykonane przewieszenie po spodniej stronie tułowia, gdzie filament praktycznie nie zawijał się do góry tak jak w przypadku Lay-Fomm. Problemem za to było wydrukowanie fragmentów łączących przednie łapy z tułowiem – były ono na tyle delikatne, że łamały się w trakcie drukowania, lub przy późniejszym odklejaniu wydruku. Mimo kilku podejść nie udało mi się poprawnie wydrukować tego modelu.
Przy wszystkich rodzajach Poro-Lay, na wielu wydrukach widoczne były nitki filamentu – pozostałość po ruchach głowicy pomiędzy różnymi drukowanymi fragmentami. Standardowo pojawianiu się takich cienkich nitek zapobiega retrakcja – mechanizm chwilowego, szybkiego wycofania filamentu w trakcie jałowego ruchu dyszy. Niestety przy Poro-Lay, mimo kilku różnych prób nie udało mi się ich wyeliminować.
Również parę razy zdarzyło mi się, że filament zawinął się w ekstruderze całkowicie go blokując. Podobny efekt miałem wcześniej przy drukowaniu z TPE – problem związany jest z konstrukcją samego ekstrudera, gdzie za zębatką radełkowaną znajduje się nieco za dużo wolnej przestrzeni, w której filament potrafi się splątać:
Płukanie w wodzie
Zgodnie z informacjami od producenta, wydruki wykonane z Poro-Lay, w zależności od rodzaju materiału należy płukać w wodzie od 1 do 4 dni. Istnieje kilka zaleceń jak usprawnić proces usuwania PVA – jest to między innymi użycie ciepłej wody i najlepiej myjki ultradźwiękowej. Swoje wydruki umieściłem w wysokich szklankach z chłodną wodą z kranu, którą co 12 godzin wymieniałem na świeżą, przy okazji sprawdzając, w jakim stanie są moje modele. Co ciekawe, już chwilę po zmoczeniu przedmioty stały się lepkie w dotyku wskutek rozpuszczania zawartej w filamencie pomocniczej substancji. Za każdym razem po 12 godzinach woda stawała się w różnym stopniu mętna (szczególnie w przypadku Lay-Fomm 40), a wydruki nabierały giętkości. Jako że rozpuszczanie PVA następuje od warstw zewnętrznych do środka, przedmioty najpierw zdobyły miękką i giętką powierzchnię, a dopiero później stały się elastyczne w całości.
Po 4 dniach wyjąłem wydruki z wody i pozostawiłem je do wysuszenia. Niestety po kilkunastu minutach zauważyłem wypływającą z nich lepką substancję – resztki niedostatecznie rozpuszczonego PVA. Jak widać, ilość wody w której płukałem modele okazała się niewystarczająca – dlatego do dalszego moczenia użyłem 3-litrowych pojemników:
Po kolejnych 2 dniach wyjąłem przedmioty z wody i obejrzałem je dokładnie przed ostatecznym wysuszeniem. Wszystkie modele zmieniły kolor z kremowego na biały, z bardzo ładnym perłowym połyskiem. Wydruki z Lay-Fomm 60, jak można było się spodziewać, okazały się najtwardsze ze wszystkich. Poza znacznym spuchnięciem na wysokość, przedmioty zachowały swój kształt oraz spójną strukturę. Można było je praktycznie zginać na pół, po czym bez żadnych uszkodzeń wracały do początkowej formy. Wydruki z Lay-Fomm 40 stały się dużo bardziej miękkie i uzyskały delikatniejszą powierzchnię. W niektórych miejscach doszło jednak do rozwarstwień i drobnych zniekształceń w ich strukturze. Jeszcze bardziej delikatne, mimo początkowej sztywności stały się modele z Gel-Lay – szczególnie w w przypadku modelu plusa, który przypominał nieco rozwarstwiającą się galaretę i strach było mocniej ścisnąć go w dłoni. Wydruki z tego ostatniego materiału po odkształceniu wolniej też wracały do początkowego kształtu.
O ile wszystkie przedmioty nabrały giętkości, żaden z nich nie stał się szczególnie rozciągliwy. W przypadku modelu ramki z Lay-Fomm 60 rozciągnięcie jednego z jej brzegów zwiększyło jego długość raptem o 2 mm (5%). Również wszystkie wydruki wyraźnie spuchły na wysokość – w przypadku plusa, mającego w oryginale 16 mm, wydruk z Lay-Fomm 60 miał 24 mm, Lay-Fomm 40 – 23 mm, a Gel-Lay – 21 mm. W płaszczyźnie X-Y wszystkie modele zachowały swoje oryginalne wymiary.
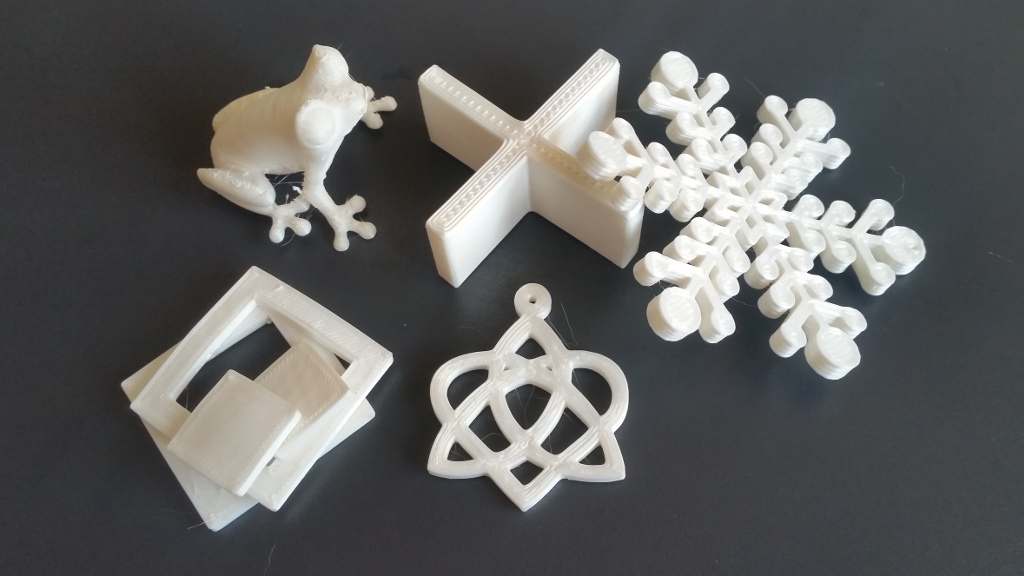
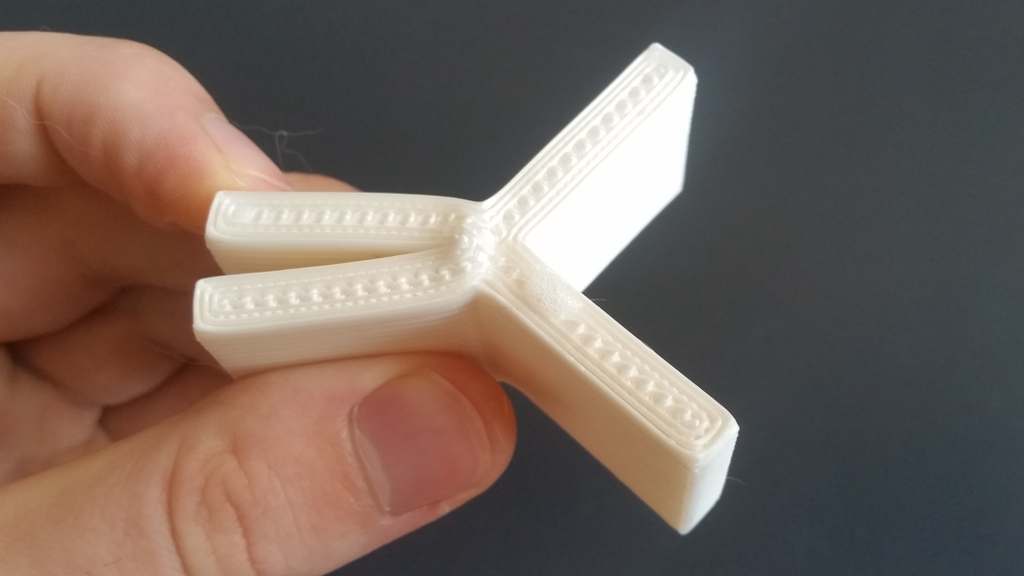
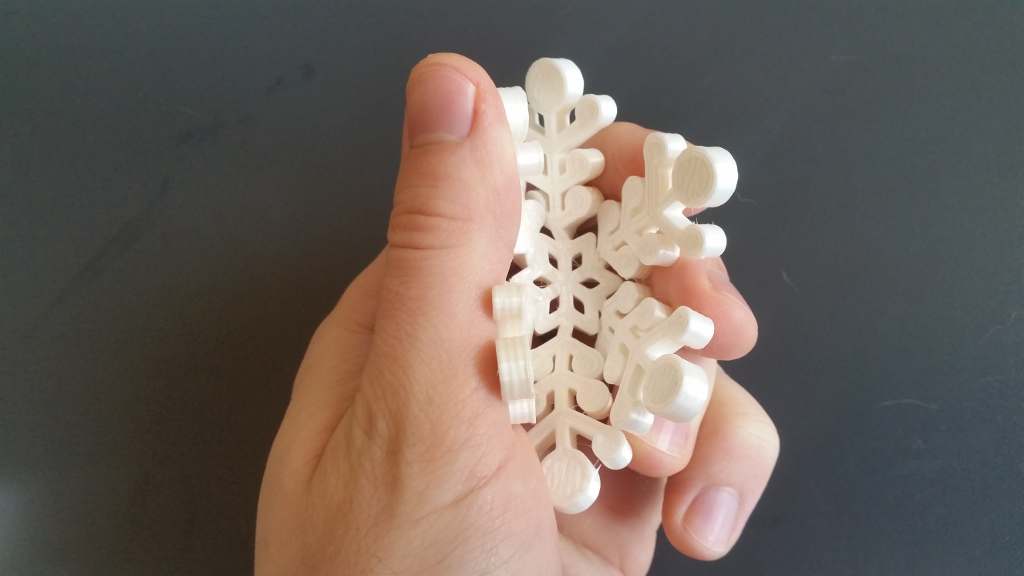
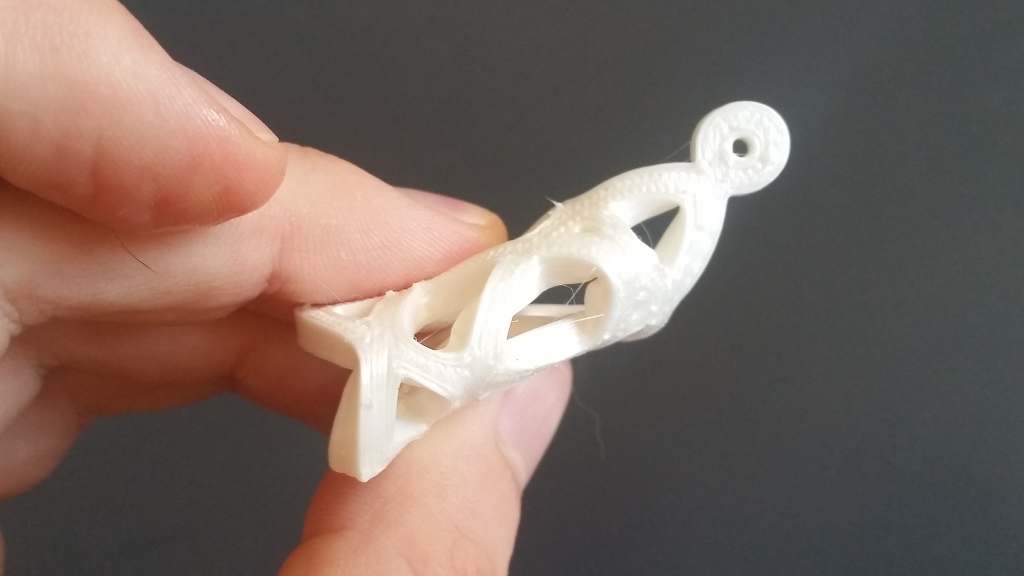


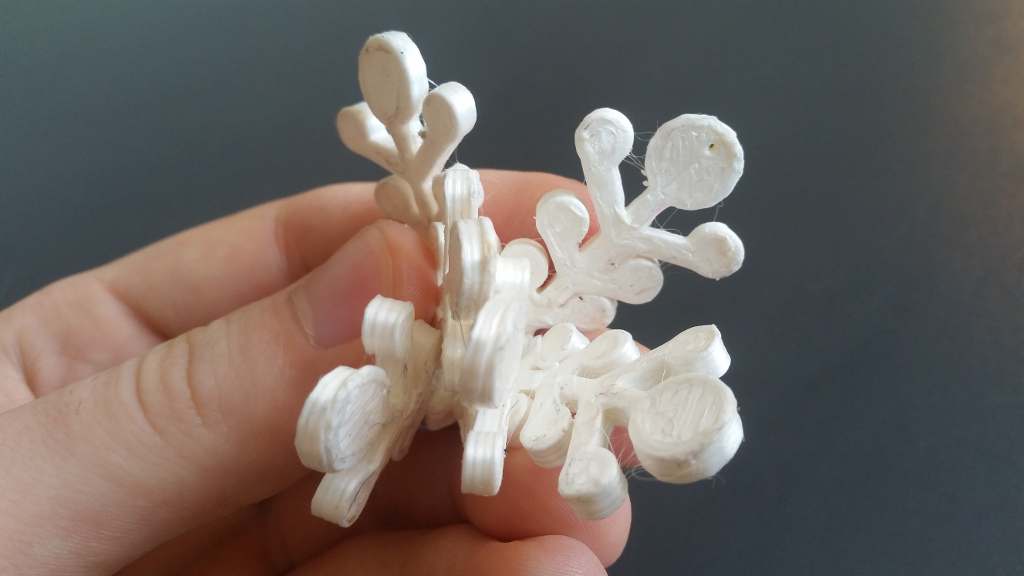
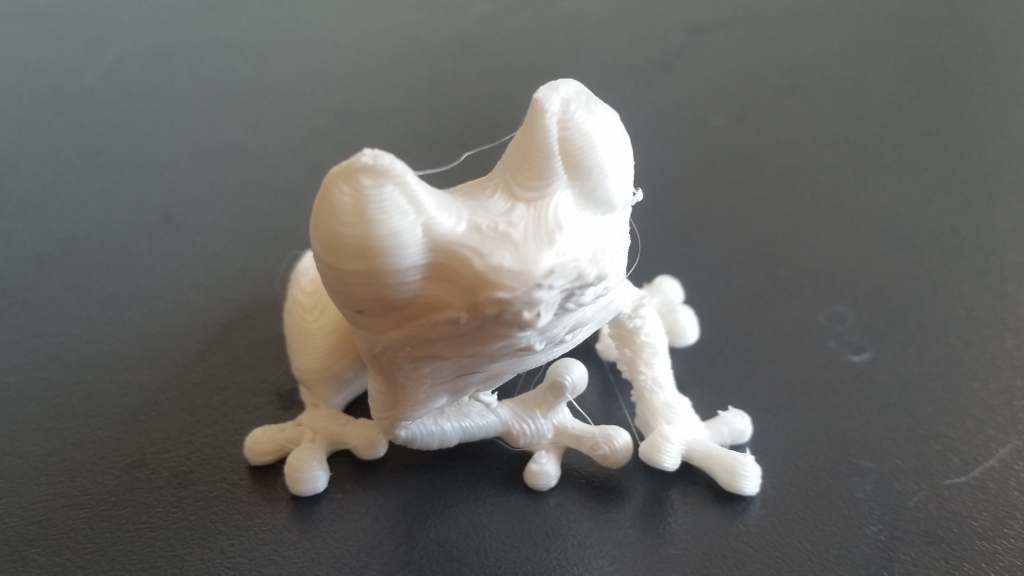


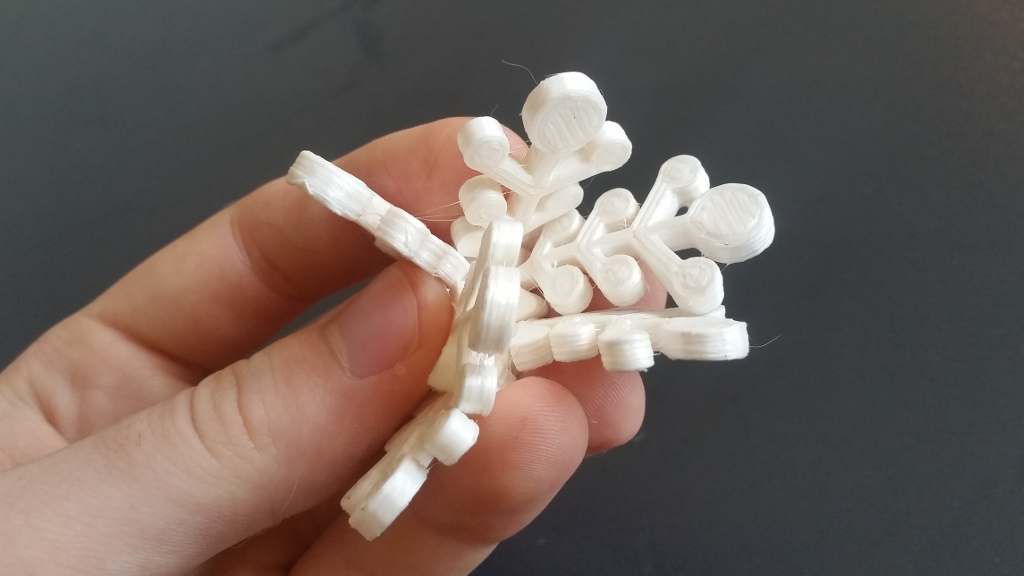

Suszenie
Mimo że z wydrukowanych plusów po ściśnięciu nadal wydobywało się nieco lepkiej piany, zdecydowałem się wysuszyć wszystkie przedmioty i zobaczyć jak będą się zachowywać po odparowaniu z nich całej wody. Przez kilkanaście minut ogrzewałem je za pomocą suszarki do włosów, a następnie pozostawiłem na 48 godzin. Jednak po tym czasie okazało się, że z jeden z plusów (Lay-Fomm 60) jeszcze nie do końca wysechł – dlatego postanowiłem poczekać jeden dzień dłużej.
Suszenie najbardziej dało się we znaki wydrukom z Gel-Lay, które mocno się skurczyły na wysokość – w przypadku plusa aż o 40% (8 milimetrów) od momentu wyjęcia z wody. W efekcie – z oryginalnego modelu o wysokości 16 mm powstał przedmiot wysoki na 13 mm. Do tego wszystkie wydruki z tego filamentu stały się twarde i sztywne, przypominając wysuszone przedmioty z rozmoczonego papieru lub plastik pomalowany białą farbą emulsyjną. Przy próbie zginania wydruki zaczynały się rozwarstwiać.

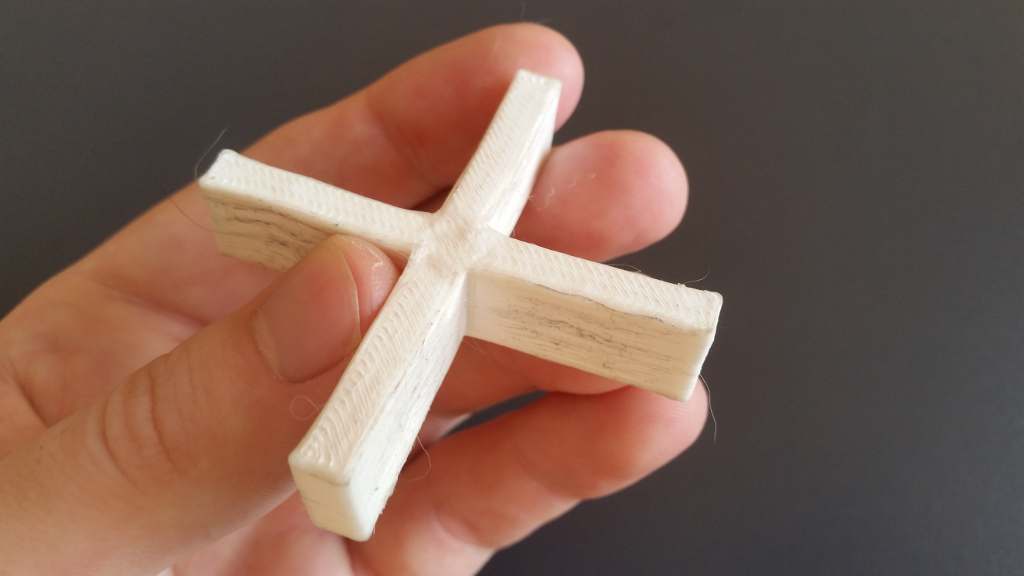
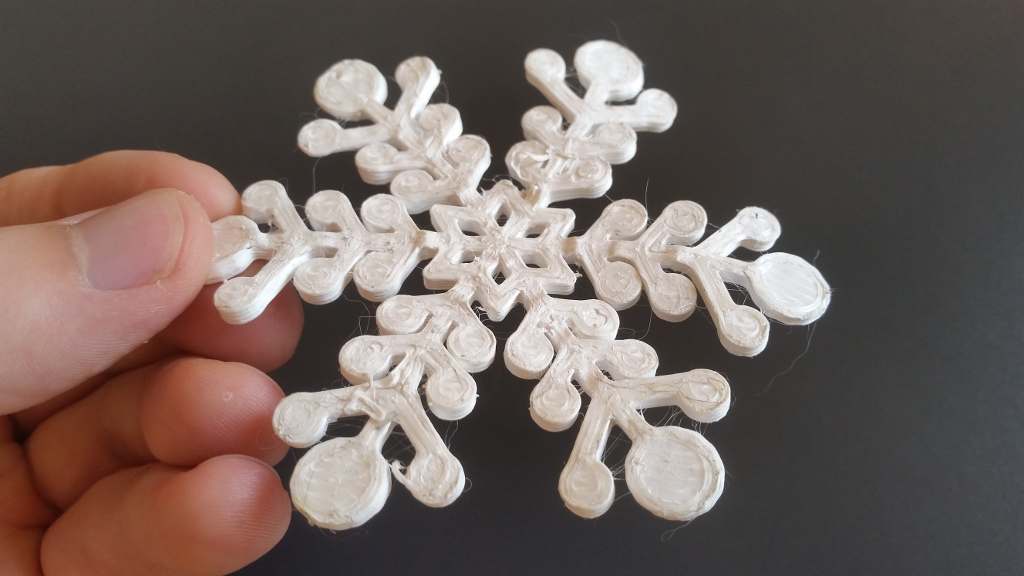

Trochę lepiej wypadły przedmioty z Lay-Fomm 40 – mimo że również się skurczyły (ponad 20%), zachowały dużo elastyczności. Ich powierzchnia trochę zaczęła przypominać syntetyczną skórę o jasno-kremowym kolorze.
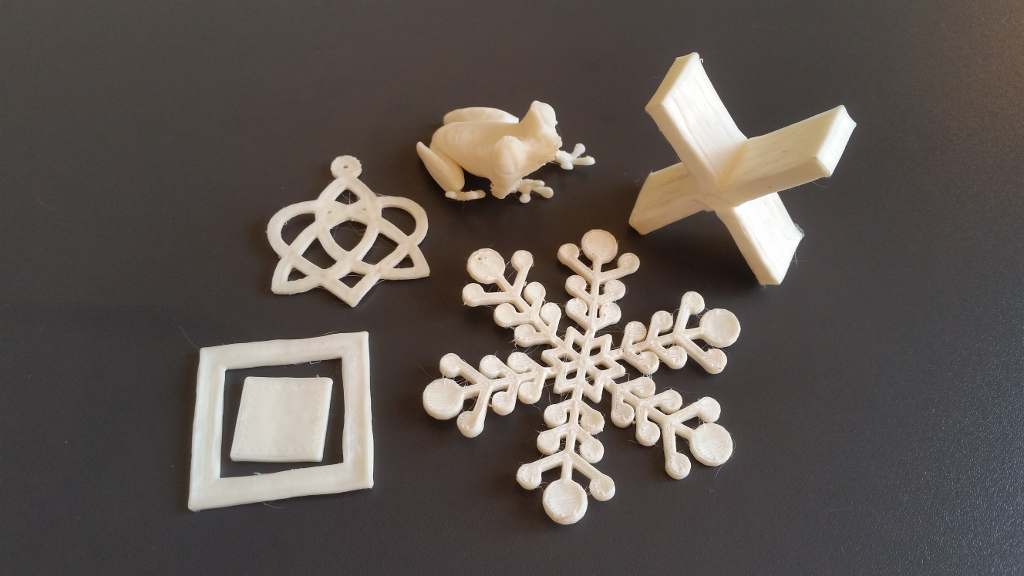



Zdecydowanie najlepiej zachowały się przedmioty z ostatniego materiału – Lay-Fomm 60. Zmalały o niecałe 20% i również pozostały w dużym stopniu elastyczne (choć nie tak bardzo jak Lay-Fomm 40). Ich powierzchnia pozostała gładka i pozbawiona zniekształceń – przypominając stan w jakim przedmioty były zaraz po zdjęciu z drukarki. Ze wszystkich wydruków w ogólnej ocenie właśnie temu filamentowi dałbym najwięcej punktów.




Kilka słów podsumowania
Pomijając problemy ze zbyt mocnym przyklejaniem wydruków do stołu, korzystanie z Poro-Lay nie jest specjalnie trudne. Jest za to bardzo czasochłonne – bez użycia dodatkowych urządzeń porządne wymoczenie i wysuszenie wydruków może zająć nawet tydzień. Z pewnością warto wziąć to pod uwagę dobierając ustawienia slicera – przy cienkich ściankach i mniejszym wypełnieniu (o ile to możliwe) wypłukiwanie PVA będzie przebiegało sprawniej.
Jeśli chodzi o zastosowania praktyczne filamentów z rodziny Poro-Lay – producent wspomina o produkcji membran, filtrów, elementów ubrań, mikropianek, gąbek i różnych innych elastycznych przedmiotów. Osobiście trudno mi znaleźć dobry przypadek użycia dla Gel-Lay, poza elementami dekoracyjnymi, gdzie specyficzna, uzyskana przy jego pomocy struktura materiału mogłaby być korzystna. Dużo większe pole popisu mają filamenty Lay-Fomm – o nieco podobnych własnościach do gumowych materiałów, jednak dużo mniej wymagające na etapie druku.
Żródła: www.3ders.org, get3d.pl